Lessons From Lodi
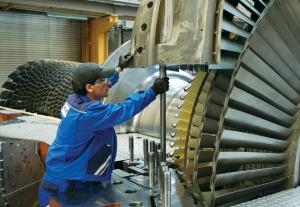
If there’s an electric power project under development that best reflects the current state of the U.S. gas turbine market, it might be the Northern California Power Agency’s (NCPA) 280-MW, natural gas-fired combined-cycle plant in Lodi, Calif.
Scheduled for startup in 2012, the plant will serve some 14 different entities, including eight area municipalities. More important, it’s the first application of a new combined-cycle plant specifically designed to operate at a wide range of loads at 57-percent-plus efficiency and deliver up to 200 MW of power to the grid in just 30 minutes.
In addition to reducing the carbon footprint of the NCPA’s membership, the system—which the manufacturer, Siemens Energy, calls the Flex Plant 30 power island—will allow the agency to react quickly to the uncertain market conditions many expect will result when state-mandated renewable energy plants begin pouring power into California’s wholesale electricity pool.
In other words, the plant will provide financial cover, a hedge if you will, against whatever California’s energy future brings.
“California’s renewable energy program will certainly bring change, but at this point we’re not sure how much,” says Ken Speer, the NCPA’s assistant general manager of generation services. “So we based our decision on the belief that a more flexible generating resource, one with a fast start capability, will be a valuable asset.”
Following the Market
Most U.S. electric utilities and independent power producers looking to add new generation share concerns similar to those at NCPA. With cap-and-trade legislation still pending, gas-fired turbines provide the lowest possible carbon footprint, next to renewable sources.
“For some participants, the Lodi plant will replace coal-based (power purchase agreements) that expire in 2012 and 2013,” Speer says. “Those contracts represent a carbon footprint of 2,100 to 2,200 lbs of CO2 per MWh, while this plant will be less than 800 lbs per MWh. So, these participants are cutting their carbon footprint by nearly two-thirds.”
And with new renewable portfolio standards now in effect in 33 states, combined-cycle plants increasingly will be called upon to serve as a back-up power source. A new plant must be able to cycle up and down efficiently, while staying within its emissions limits, even at low load operation.
It’s not surprising then, that when it comes to the latest original equipment manufacturer (OEM) gas turbine offerings, the new catchphrase is “operational flexibility.” Such suppliers as Siemens, General Electric (GE) and Alstom are rolling out an assortment of upgrades to existing machines that will boost output and efficiency and enhance the ability to react quickly to changing load requirements.
“In the U.S. roughly 45 percent of the generating capacity is more than 30 years old and a number of those plants will need to be replaced near term, even if economic growth remains sluggish,” says Patrik A. Meier, Alstom Power’s gas turbine product manager. “With the delays in permitting coal and nuclear plants, a natural gas-fired turbine plant represents a comparatively quick solution.”
GE, which also was in the running for the Lodi project, has introduced a new Frame 7FA gas turbine that will generate 211 MW, a 36-MW increase over the current 7FA in simple cycle operation. When configured in a rapid response two-unit combined-cycle arrangement, the company says the system will be able to deliver 150 MW to the grid in just 10 minutes.
The combined-cycle configuration, GE adds, will be able to achieve a fuel cost savings of more than $2 million a year with natural gas at $6 per MMBtu when compared to a similar plant with an earlier version of the 7FA, and avoid the annual emission of more than 19,000 metric tons of CO2 compared to previous performance.
Key to the new turbine design, the company says, is: 1) a more efficient compressor that increases airflow; 2) enhanced fuel efficiency via three-dimensional aerodynamic airfoils; and 3) a hybrid radial compressor diffuser. Three variable stator vane stages support unit flexibility by allowing the control system to adjust compressor airflow to meet varying fuel and ambient conditions, or in response to changing operating conditions.
“Though we’re seeing slower sales overall due to the economy, the gas-fired power plant is going to be a strong segment going forward,” says Jim Donohue, gas turbine marketing manager at GE. “With the new 7FA, we’ve given customers a tool to respond to potential emissions legislation. Plus, it has a fast start capability, so it can deliver power quickly to the grid while striking a balance between efficient operations and emissions compliance.”
Alstom Power has introduced upgrades to its 193-MW, 60-Hz GT24 turbine as well. It too has focused on optimizing the unit’s compressor, increasing the airflows through it and facilitating an increase in combined- cycle performance of nearly 9 MW, by increasing the unit’s turbine inlet temperatures.
The turbine also is part of Alstom’s latest 60-Hz KA24 combined-cycle power plant offering, which is comprised of a three casing, double flow low-pressure steam turbine, air-cooled generator, and water-cooled condenser, and a three-stage reheat, horizontal type heat recovery steam generator (HRSG). The integrated system, Alstom says, will produce power with efficiencies exceeding 57 percent, with a turndown capability to near 20 percent and full start-up in less than 50 minutes.
“When we introduced the GT24 in the 1990s, the machine was ideally suited to serve the combined-cycle market,” says Mark Stevens, KA24 product manager. “The sequential combustion system provided the high exhaust temperatures needed to support combined-cycle operation at a variety of loads, which combined with three rows of inlet guide vanes supports high partial-load efficiency. When we first introduced it we were looking for good all-around performance, not just high baseload operation. From that viewpoint, it was a little ahead of its time.”
Flexible Tech
Today’s big issue, of course, is cycling. Due to changing market fundamentals, fewer gas turbine combined-cycle plants are running at full base load operation anymore. In many cases, cycling duty has become the new normal.
As a result, combined-cycle plants need to operate efficiently at low load and, when necessary, ramp up quickly without negatively impacting emissions, fuel or O&M costs. That needn’t be a problem, according to the OEMs, because of these new integrated offerings.
With a traditional gas turbine-powered combined-cycle plant, the startup always, by necessity, has been gradual in order to protect the downstream steam cycle piping and components within the HRSG and the gas turbine. Start up too quickly and the components will be thermally stressed, which degrades and weakens the metals and drives up O&M costs.
Under its combined-cycle configuration, GE’s Donohue says the gas turbine is decoupled from the HRSG and steam turbine to enable a rapid response to changing load demand. Instead of bringing the entire system up slowly to avoid over-stressing metal piping and other components, the bottoming cycle hardware associated with the HRSG and steam turbine is warmed up separately.
A twin gas turbine set is brought up to full output quickly, delivering some 150 MW of electricity to the grid in about 10 minutes, compared to nearly an hour under previous combined-cycle configurations. Equally important, Donohue says, is that bringing a turbine to full output quickly cuts startup emissions by half. Therefore, he says, the configuration is ideally suited to backup duty for RPS-mandated intermittent renewable sources.
“With the HRSG and steam turbine cycle, you’ve got a lot of steel,” Donohue says. “With the system’s rapid response capability, you let the HRSG and steam turbine warm up to about 30 percent, while the GT goes right to full load. It’s done through a combination of new controls, piping and valves. The overall system efficiency remains the same.”
GE will demonstrate the new combined-cycle plant at the 586-MW Oakley Generating Station in Oakley, Calif., being developed by Radback Energy Inc. When the plant is finished, Radback will transfer ownership to PG&E.
The Siemens plant at Lodi also integrates a number of features to facilitate fast startups, including a three pressure reheat HRSG with Benson once-through technology, high capacity steam attemperation and full capacity steam bypass systems. Simply put, steam initially produced in the HRSG is bypassed to the condenser until the steam turbine is ready to accept it, and then the steam turbine is monitored for faster ramp rates. Full combined-cycle plant load, Siemens says, could be reached in as little as 45 minutes.
“It’s not that the turbine design is radically different. The difference is in the steam cycle.” says John M. Wilson, vice president of new unit sales at Siemens North America. “If you cut the gas turbine startup time, you can cut the startup emissions by well over 50 percent of a non Flex-plant, plus you have the associated fuel savings. But the real design changes are to the steam cycle in the HRSG components, like the steam valving and our T-3000 integrated control system.”
The generator is motored to bring the gas turbine up to speed (i.e., less firing of the gas turbine than is required when using a starting motor) and the unit can generate power with a low NOx combustor to deliver NOx emissions of 9 ppm. With the installation of SCR and CO2 catalysts, stack emissions compliance can be reached in about 30 minutes.
“You can get 10 to 30 MW a minute from a large industrial gas turbine,” Wilson says. “With the more traditional combined-cycle plants, the HRSG/steam turbine cycle limits the gas turbine to a much slower rate. So with the Lodi project, we’ve designed the steam cycle with enough flexibility to accommodate the gas turbine.”
Though the GT24 has been around for more than a decade, Alstom’s Meier says its dual combustor design always has been ideally suited to cycling duty. For example, he says, the turbine can maintain low load operations on only one of the two combustor stages. The turbine still delivers enough heat to keep the water-steam cycle, including the HRSG and steam turbine operating, allowing the combined cycle to be turned down as low as 20 percent, while still meeting emissions requirements.
“In today’s energy markets customers need a plant that can react quickly to take advantage of the most profitable hours in the market,” he says. “With our integrated combined-cycle concept, we can reach full system output in less than 50 minutes, compared to the traditional 60 to 90 minutes.”
If necessary, he adds, the system’s HRSG can be fitted with additional gas burners to quickly provide additional output, if and when it’s necessary. “If you need more power, you ignite the supplementary burners. In that case, the overall system efficiency declines, but you can boost the output,” he says.
O&M Squeeze
OEMs are adding such flexibility to their plant designs because they expect natural gas to play an increasing role across various load profiles, from peaking to base load operations. This reliance on gas is driven, in part, by the expansion of unconventional gas sources (See “Gas Market Outlook”). According to a report released last year by the Colorado School of Mines, the country’s natural gas reserves estimates rose to 2,074 trillion cubic feet in 2008, up from 1,532 trillion cubic feet in 2006. With this supply increase due in particular to new domestic shale gas opportunities, the availability of natural gas appears stable.
At the same time, however, OEMs understand uncertainties affecting gas sources—including imported liquefied natural gas (LNG)—and they’ve taken steps also to address potential fuel composition issues, should they arise. Each company says its machines will adjust automatically to changes in chemical composition—as opposed to shutting the unit down to address burner components and settings—if a large amount of regasified LNG enters the system, for example.
OEMs also have applied newer, more protective coatings to extend the operating life of key internals, particularly those exposed to the higher operating temperatures in the hot gas path; such high temperatures are needed to increase unit output and efficiency. Further, they have established remote, 24-7 diagnostics phone centers with trained technicians using Web-enabled technology to help resolve operations issues if or when they arise.
In a somewhat novel approach, Alstom has begun offering a GT24 MXL upgrade package that allows plant operators to switch online between two turbine operating modes. The “M” mode increases power output, while the “XL” backs it off, thereby extending component life. An operating data counter tracks operations in both modes to give the customer a running tally of the unit’s start-stop operations, which helps in scheduling the unit’s next maintenance outage.
“When market demand is high you can instantly switch to M mode for maximum power and efficiency,” Meier explains. “When demand is lower, you can switch to XL mode with a temperature drop that reduces the operating stress on components. Regularly operating in this mode can extend a unit’s inspection interval by up to 4,000 equivalent operating hours.”
Of course all these developments come at a price.
Though OEMs acknowledge added performance measures will boost the cost of their machines and combined-cycle systems, they demur when asked by how much. Whether U.S. power producers will be willing to pay the extra premium hinges on some of the very uncertainties that are driving the need for flexibility in the first place. In other words, depending on how market conditions and regulatory factors evolve, the value of these new systems might increase substantially.
“The investment is prudent in high-priced emissions markets for NOx, CO2 and VOCs,” Siemens’s Wilson concludes. “CO2 mitigation will make it worth the added investment everywhere.”
---
Assuming Control: Today’s I&C Technology
Many generators are hoping to get more flexibility out of existing power plants by swapping out their instrumentation and controls systems. Others are being forced in this direction as their old systems reach the end of their useful lives. Fortunately, indications are it’s a buyer’s market, with fierce competition among suppliers to expand functionality, accelerate installation and contain costs.
“It’s pretty competitive right now. Due to the economy, there are fewer retrofits,” says Kevin Kochirka of ABB’s power generation division. “We’re a DCS (distributed control system) supplier, and we’re seeing PLC (programmable logic controller) suppliers bidding on our jobs. You never used to see that.”
Citing obsolescence issues, OEMs who supplied the first wave of digital hardware and software controls in the 1980s and 1990s are eliminating parts and service support to introduce replacement systems. Customers who keep using their old systems must buy replacement parts from third-party suppliers, often at higher prices, and handle maintenance in-house.
Further, with a growing number of gas turbine combined-cycle plants now being cycled to meet changing market conditions, experts say older control systems could present reliability issues as operators push them beyond their intended design limitations.
“Older control systems weren’t really designed for cycling duty,” says Andy Dieball, I&C product manager with Siemens Energy. Specifically, older systems employ a simplex-type controls arrangement, which have a single connection between, for example, the control panel and a valve. By contrast, new systems have redundancy measures built-in, essentially providing multiple connections to the valve so if one fails, another takes over.
“There are many other technical improvements available, like turbine vibration monitoring and predictive maintenance,” says Bill Lauer, business development manager with Emerson Controls. “For example, the customer can simulate operational changes to measure the impact on turbine performance.”
Additionally, new systems offer greater longevity and serviceability than black-box systems did in the past. Instead of proprietary logic that only the vendor can service, I&C manufacturers today are rolling out simpler controls featuring open architecture designs that will make it relatively easy to expand or migrate to newer technologies. This should help avoid the obsolescence issues that plagued older designs.
And the demands of competition have driven vendors to optimize their installation processes, to perform complete system replacements in even the narrowest of outage windows. Such was the case when Siemens Energy replaced an early-1990s DCS at a 285-MW Cogentrix cogeneration facility in Carneys Point, N.J.
The plant, which consists of two coal-fired boilers and a steam turbine, delivers 20 MW to an adjacent industrial host, E.I. DuPont De Nemours and Co. Since DuPont operates 24-7, 365 days a year, it couldn’t live with a prolonged outage for the DCS upgrade. As a result, it gave Cogentrix just 36 hours to complete the change-out.
Siemens assembled the new system at its Alpharetta, Ga., facility and had technicians simulate the replacement, step by step, right down to the new cabinets.
“It was truly remarkable. When it was time to go everybody did their tasks in parallel,” says Steve DiCarlo, Cogentrix plant manager. “They ripped the old DCS out, put the new one in and we brought one of the units up to produce steam, all within 36 hours. I have to give them a well-deserved ‘touché.’”