Exelon Chief Operating Officer Mike Innocenzo sat down with PUF's Steve Mitnick last week.
Clean Power Economics
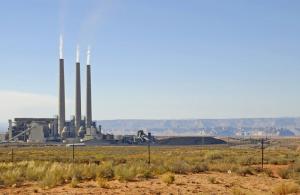
Rapid changes to electric power markets are posing new challenges to fossil-powered generating facilities across the country. Baseload coal-fired units, designed to operate virtually 24/7, now often face cycling duty due to increased generation from natural gas and renewable sources.
Coal plants, in particular, are facing retirement in ever greater numbers. Can refurbishing existing environmental controls—including measures that support cycling duty by ensuring environmental compliance over a much greater operating range—enhance the value of a coal-fired asset and prolong its operating life?
We recently spoke with Tom Alley, vice president of generation at the Electric Power Research Institute (EPRI), about how the organization is helping its members evaluate their fleets and establish long-term strategies for each asset class.
The first of this two-part series (see "Long-Term Assets in a Real-Time World") focused on ways to enhance generating asset value by leveraging new technologies to reduce operations and maintenance (O&M) costs. In Part II, we focus on using technology to enhance an asset’s environmental compliance.
FORTNIGHTLY Environmental compliance obviously has a major impact on power plant economics. What are your members looking for in this area?
Tom Alley, EPRI: The decisions our members have to make are unique because they’re looking at power plants or specific units with regards to their specific purpose—their support of the grid, their location, and their startup capabilities.
There are so many variables that go into deciding how to best manage a fleet. With unit cycling becoming so prevalent, we’re looking at technologies that maintain or enhance the performance of existing environmental controls across a range of loads. If successful, the cost of operating a unit will be reduced and that, in turn, will have some bearing on how a member-utility may view that asset.
One important factor is environmental flexibility. Environmental controls can limit the ability to operate a plant in a variety of modes, be it faster starts or deeper turndown ratios. So we’re looking at how the controls need to respond to make a unit more flexible. We want to remove some of those barriers to facilitate broader operational parameters.
So we’re looking at technologies that will expand that window, from manufacturing activated carbon on-site to capture mercury, to enhancing the performance of precipitators and SCRs. Rather than replacing existing controls with new, more expensive technologies, they can more economically operate a unit with the controls already in place.
FORTNIGHTLY Mercury is a big issue right now. How would manufacturing activated carbon on-site reduce a unit’s operating costs?
Alley: If a utility can produce activated carbon on its own at the plant site, it can reduce the cost of activated carbon by roughly 50 percent. Activated carbon is a commodity. If you can reduce that cost by half, you could potentially move a coal unit higher in the economic dispatch pecking order. At the very least, you might be able to make that asset economical to operate.
The process is already commercial. Powdered activated carbon (AC) is pneumatically injected from a storage silo into the flue gas ductwork, where it adsorbs mercury and is collected in the plant’s particulate collector.
In our study, were taking pulverized coal produced at the plant and processing it in an entrained flow reactor to form AC that can then be injected directly into the power plant flue gas—either upstream of a particulate control device or between an electrostatic precipitator (ESP) and a downstream fabric filter—to capture flue gas mercury.
Right now we’re sponsoring major AC demo projects at AEP’s Pirkey Plant and Great River Energy’s Coal Creek Plant. The Pirkey demo is under way right now and should be completed before year end. Results to date are very encouraging, with no major issues. Based on the project schedule, we should have a report available in early- to mid-2014.
FORTNIGHTLY How about expanding, in effect, a unit’s operating range while remaining in environmental compliance? How can environmental controls be improved to facilitate that?
Alley: By extending the operating range of the SCR’s catalyst, a utility looking to cycle certain units could save money by operating at even lower loads.
A lot of catalyst manufacturers have curves and operational limits around the catalyst that restrict how low the unit can be turned down. We’re doing research around catalyst poisoning or contamination to see whether we can broaden that operational window to accommodate periodic reduced load operation beyond normal low-load limits. The ability to reduce unit output while still maintaining emissions performance would reduce operating costs and enhance the unit’s standing in the fleet.
FORTNIGHTLY Where are those studies being conducted and when will the results be public?
Alley: At TVA, which is currently reviewing a Phase I summer low-load test report. The initial load limit was about 700 MW on a 1,300-MW unit. Now TVA is considering Phase II Autumn testing over a weekend at loads reduced to 500 MW and potentially 400 MW. Those tests are easier to do now that the summer season has been concluded.
Phase II testing will assess potential ammonium bisulfate formation impacts, including catalyst activity tests by layer, SCR inlet/outlet speciated Hg measurements, and continuous ammonia slip measurements at the SCR outlet. SCR performance recovery upon resumption of full load operation will also be monitored.
Regarding SCR catalyst R&D, we have an active program assessing issues associated with turndown impacts, including the factors that impact mercury oxidation, catalyst management for both NOx and mercury control, advanced process control, and optimization of catalyst performance.
FORTNIGHTLY You also mentioned precipitators. What are you doing there?
Alley: We’re examining a new system called PMScreen, which is an electrostatic precipitator (ESP) add-on device designed to ensure compliance with the EPA’s Mercury and Air Toxics Standards (MATS) regulations. It’s basically a movable screen just downstream of the existing ESPs that captures particulate matter not captured in the ESP. Pilot-scale testing to date has shown that a properly selected filter can reduce particulate matter emissions to very low levels, while still maintaining a reasonable pressure drop.
FORTNIGHTLY How about new technology, are you working with suppliers and/or OEMs?
Alley: Yes and no. We have research underway that examines advanced coal burning technologies. This research is pretty far reaching—it basically involves the next generation of coal plants. For example, we have a couple of gasification projects underway here in the U.S. and we’re also looking at chemical looping.
As far as building new coal plants in the U.S., we’re of the opinion that it’s going to be pretty difficult to accomplish what we’d like to see by just tweaking supercritical coal plants. So we’re trying to keep our finger on the pulse and let our members know what’s going on in the industry with regards to new technologies.
With regards to gas turbine technology, we don’t do as much with the GT manufacturers because those are pretty closely guarded trade secrets.
FORTNIGHTLY It certainly looks like electric power resource planning is a difficult job right now.
Alley: Yes, it’s a very difficult environment. If we were to look back ten years we never would have projected natural gas prices at $3 MMBtu. Fuel pricing and regulatory policy will continue to drive some of these decisions. Plus, we’ve seen flat to decreasing demand, which only adds to the uncertainty. And that makes decision-making all the more difficult.
ABOUT THE AUTHOR Scott M. Gawlicki is Fortnightly’s contributing editor, based in West Hartford, Ct.
ABOUT THE SOURCE Tom Alley is responsible for EPRI’s R&D team, which is focused on research, development, and the application of fossil technologies for both existing and future generating assets. He has 29 years of experience in the energy industry, and his experience includes fossil and nuclear power. He joined EPRI in 2007 as senior program manager for major component reliability R&D, and most recently served as director of advanced generation research, which includes renewable generation, carbon capture and storage, generation planning, and industry technology demonstrations. Before joining EPRI, Alley worked at Duke Energy, leading a centralized corporate team of metallurgists, engineers, and technical personnel responsible for the evaluation, inspection, and repair of nuclear power plant components.